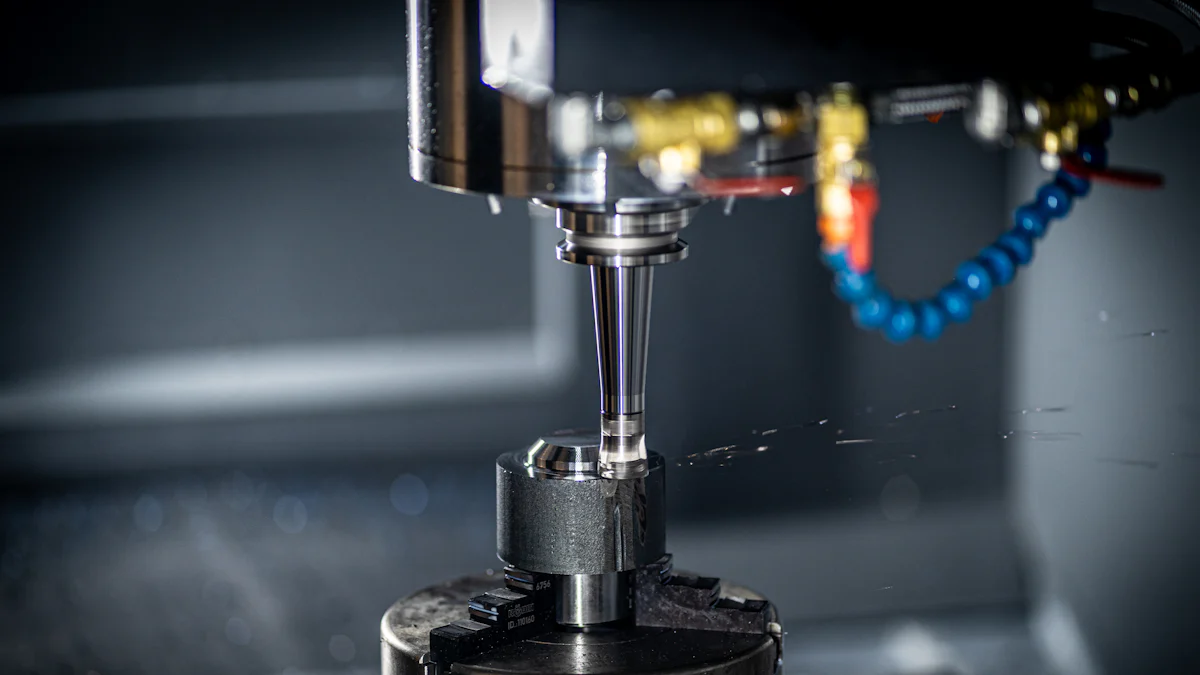
Imagine creating parts so precise that even the smallest error could disrupt an entire system. This is the power of precision machining. It’s a process where material is carefully removed to achieve exact dimensions and tight tolerances. You rely on this technology every day, whether it’s in the car you drive or the medical devices that save lives.
Precision machining transforms industries by delivering unmatched accuracy and efficiency. Advanced techniques like CNC machining ensure consistent quality, reducing waste and lowering costs. In fact, the precision parts market is projected to grow by 12% by 2024, driven by its ability to meet the demands of modern manufacturing. From surgical instruments to high-performance engine components, precision machining shapes the future of innovation.
Key Takeaways
- Precision machining makes parts that fit perfectly and work well.
- CNC machining improves speed, cuts waste, and saves money for companies.
- It helps create complex designs for planes, medical tools, and gadgets.
- Tight measurements are key for safety in cars and airplanes.
- Using automation and AI makes machining faster and more accurate.
- Recycling and energy-saving tools make machining better for the planet.
- It works with many materials like metal, plastic, and composites.
- Precision machining helps businesses stay ahead and solve future problems.
What Is Precision Machining?
Definition and Key Features
Precision machining is the art of creating parts with exceptional accuracy. It involves removing material from a workpiece to achieve exact dimensions and tight tolerances. This process ensures that every component fits perfectly and performs flawlessly. You’ll find its impact in industries where precision is non-negotiable, such as aerospace, medical devices, and electronics.
What makes precision machining stand out? It’s all about the details. Here are the defining characteristics that set it apart:
- Tight tolerances that ensure minimal deviation from design specifications.
- High accuracy, essential for parts that must interconnect seamlessly.
- High repeatability, producing identical parts every time.
- Low production costs due to reduced material waste and automation.
- Speed and efficiency, delivering results faster than traditional methods.
- Enhanced safety by minimizing human error through advanced technology.
These features make precision machining a cornerstone of modern manufacturing, helping you achieve results that were once thought impossible.
How Precision Machining Works
Precision machining is a step-by-step process that transforms raw materials into finished products with unmatched accuracy. Each step plays a vital role in ensuring the final product meets exact specifications. Here’s a breakdown of the key steps involved:
Key Step | Explanation |
---|---|
Regular Maintenance | Cleaning and tool replacement reduce wear, ensuring machines produce accurate parts and minimize defects. |
Selection of Cutting Parameters | Optimizing cutting speed, feed rate, and depth of cut ensures minimal tool wear and stable cutting conditions. |
Understanding Material Properties | Knowledge of material hardness and consistency helps improve machining accuracy and meet precise tolerance limits. |
Programming and Software Utilization | Accurate CAD models and CAM toolpaths guide CNC machines, minimizing errors and ensuring conformity to design. |
Equipment Design and Quality | High-quality CNC machines with rigidity and precision produce parts that conform to tight tolerances. |
Technological Advancements | Advanced CNC machinery and real-time monitoring enhance accuracy, allowing for precise adjustments during machining. |
Measurement System Analysis | Evaluating the measurement system ensures reliable results and identifies sources of error, maintaining target tolerances. |
By following these steps, precision machining delivers consistent, high-quality results. It’s a process that combines technology, expertise, and attention to detail to bring your designs to life.
Differences Between Precision and Traditional Machining
Precision machining and traditional machining may seem similar, but their outcomes are worlds apart. Precision machining focuses on achieving perfection, while traditional methods often prioritize speed and simplicity. Here’s how they differ:
- Tight Tolerances: Precision machining minimizes deviations from CAD designs, ensuring flawless results.
- High Accuracy: It’s essential for parts that must interlock or function together without errors.
- High Repeatability: Every part produced is nearly identical, reducing defects and ensuring consistency.
- Low Production Costs: Automation and fewer defects lower material and labor expenses.
- Speed and Efficiency: Advanced robotics and CNC systems complete tasks faster, often eliminating the need for secondary processes.
- Safety: Precision machining reduces human error, allowing workers to focus on skilled tasks.
When you choose precision machining, you’re investing in quality, efficiency, and reliability. It’s the difference between “good enough” and “exceptional.”
Importance of Precision Machining in Manufacturing
Achieving High Accuracy and Quality
Precision machining plays a vital role in delivering exceptional accuracy and quality in manufacturing. You see its impact in industries where even the smallest error can have significant consequences. For example:
- In medical device manufacturing, precision machining ensures surgical instruments and implants meet exact specifications, safeguarding patient safety.
- Automotive manufacturers rely on it to produce engine parts and transmission components, enhancing vehicle performance and longevity.
- The aerospace industry depends on precision machining to create parts that meet strict tolerances, improving efficiency and reliability.
By using advanced tools and techniques, precision machining allows you to achieve results that are consistent and flawless. This level of accuracy ensures that every component fits perfectly, reducing the risk of malfunctions and improving overall product quality. Whether it’s a life-saving medical device or a high-performance car engine, precision machining guarantees excellence.
Supporting Complex and Innovative Designs
Innovation thrives when you have the tools to bring complex ideas to life. Precision machining empowers you to create intricate designs that were once impossible to manufacture. Industries like aerospace and healthcare benefit greatly from this capability:
- Multi-axis machining and high-performance cutting tools enable the aerospace sector to produce lightweight, high-strength parts such as turbine blades and structural components.
- In the medical field, precision machining is essential for crafting surgical instruments, implants, and diagnostic devices. These components require tight tolerances and complex geometries to ensure effectiveness and safety.
- Computer-aided manufacturing allows you to design and produce parts with unparalleled precision, supporting groundbreaking advancements in technology and medicine.
When you embrace precision machining, you unlock the potential to innovate without limits. It gives you the freedom to explore new possibilities and deliver products that push the boundaries of what’s achievable.
Reducing Waste and Enhancing Efficiency
Precision machining doesn’t just improve quality; it also helps you minimize waste and maximize efficiency. By using advanced techniques, you can reduce material usage and lower production costs. Here’s how it benefits both the environment and your bottom line:
- Energy-efficient machine tools consume less power, saving you money while reducing your carbon footprint.
- Eco-friendly materials, such as biodegradable substances and recycled metals, contribute to sustainable manufacturing practices.
- Recycling programs for metal scraps and coolant help you minimize waste and reuse valuable resources.
- Renewable energy sources, like solar and wind, can power machining processes, further reducing environmental impact.
By adopting precision machining, you not only create high-quality products but also contribute to a greener, more sustainable future. It’s a win-win for your business and the planet.
Processes and Techniques in Precision Machining
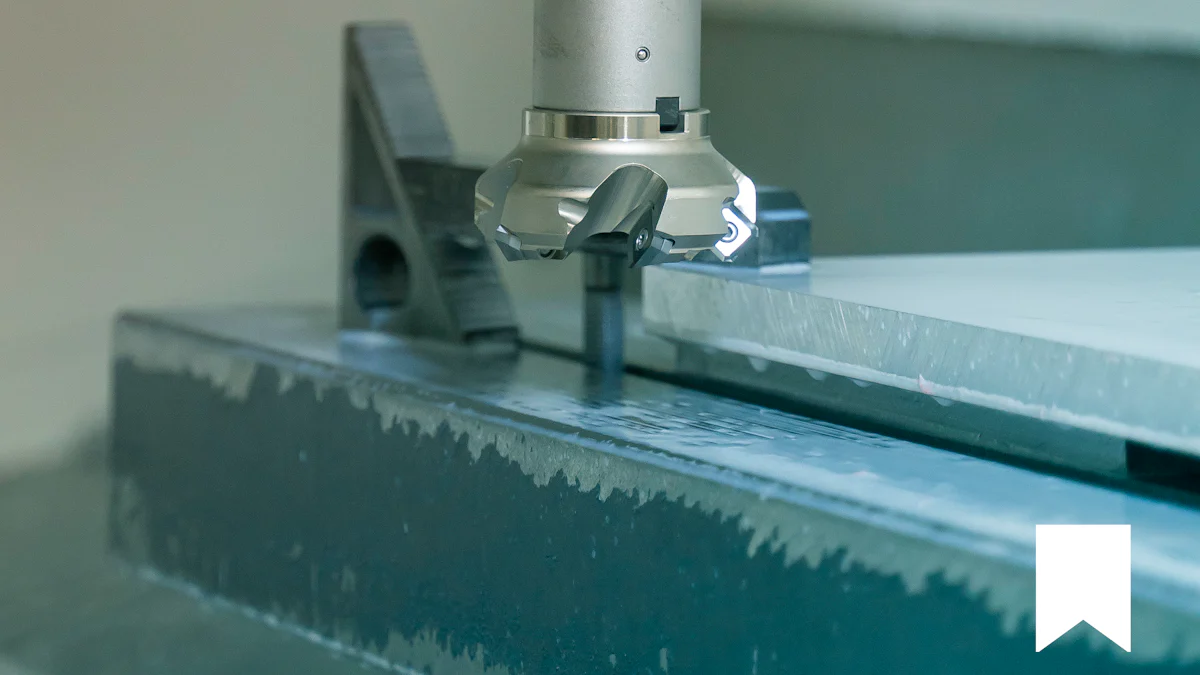
Precision machining relies on advanced processes and techniques to achieve exceptional accuracy and efficiency. Each method plays a unique role in transforming raw materials into high-quality components. Let’s explore some of the most impactful techniques.
CNC加工
CNC (Computer Numerical Control) machining revolutionizes manufacturing by automating precision tasks. It uses pre-programmed software to control tools and machinery, ensuring consistent and flawless results. This technique is ideal for producing complex parts with tight tolerances. Here are some of the most commonly used CNC machining methods:
- CNC Laser Machining: A high-frequency laser beam cuts or engraves materials, suitable for both metals and non-metals.
- CNC Mill Turning Centers: Combines milling and turning operations in one machine, boosting efficiency.
- CNC Milling: Rotating cutting tools remove material, perfect for intricate parts like engine blocks.
- CNC Turning: A lathe machine creates cylindrical shapes, essential for components like crankshafts.
- Multi-axis Machining: Tools move in multiple directions, enabling the creation of complex designs.
- Swiss Machining Techniques: Produces small, precise parts with tight tolerances.
- Precision Grinding: Focuses on achieving accuracy for small dimensions.
CNC Milling
CNC milling uses rotating cutting tools to shape materials into precise forms. You can rely on this method for creating intricate designs, such as engine blocks or molds. Its ability to handle complex geometries makes it indispensable in industries like aerospace and automotive. The process ensures high repeatability, so every part meets exact specifications.
CNC Turning
CNC turning specializes in crafting cylindrical components. A lathe machine rotates the workpiece while a cutting tool removes material. This technique is perfect for producing parts like crankshafts and shafts. It delivers exceptional accuracy and smooth finishes, ensuring your components perform flawlessly.
Electrical Discharge Machining (EDM)
Electrical Discharge Machining (EDM) offers a nontraditional approach to precision machining. It uses electrical discharges to erode material from a conductive workpiece. The process involves two electrodes separated by a dielectric liquid. When the electrical field strength becomes sufficient, the dielectric breaks down, allowing current to flow and remove material.
EDM stands out for its ability to machine hard materials like titanium and nickel alloys. It applies no force to the workpiece, enabling extremely tight tolerances. You’ll appreciate its advantages, including cost savings, consistent precision, and faster time to market. This method eliminates tool wear and reduces the need for additional machining, making it a game-changer for industries like aerospace and medical devices.
Grinding and Polishing
Grinding and polishing refine surfaces to achieve smooth finishes and precise dimensions. Grinding removes material using abrasive wheels, while polishing enhances the surface quality. These techniques are essential for applications requiring high accuracy and aesthetic appeal. You’ll find them used in creating medical implants, optical components, and decorative finishes. By combining these methods, you can achieve both functionality and visual perfection.
Laser Cutting and Engraving
Laser cutting and engraving bring a new level of precision and creativity to manufacturing. This technique uses a focused laser beam to cut or engrave materials with incredible accuracy. Whether you’re crafting intricate designs or producing functional components, laser technology empowers you to achieve results that were once unimaginable.
One of the most remarkable benefits of laser cutting is its high precision. You can create intricate cuts and detailed designs with tight tolerances, making it perfect for complex shapes. This level of accuracy ensures that every piece meets your exact specifications. Whether you’re working with metals, plastics, or composites, laser cutting delivers consistent quality across a wide range of materials.
Laser cutting also stands out for its minimal material contact. The laser beam doesn’t physically touch the workpiece, which reduces the risk of distortion or mechanical stress. This feature is especially valuable when working with delicate or heat-sensitive materials. You’ll notice that the edges are smooth and clean, eliminating the need for extensive post-processing. This saves you time and enhances the overall efficiency of your production process.
Another advantage is the versatility of laser cutting and engraving. You can use it for a variety of applications, from creating decorative patterns to producing industrial components. The process integrates seamlessly with CNC machines, allowing for automated production. This compatibility boosts efficiency and ensures repeatable results, whether you’re prototyping or scaling up to full production.
Laser cutting also shines in terms of speed and setup. The process requires minimal adjustments, so you can start production quickly. This efficiency helps you meet tight deadlines without compromising quality. Additionally, the technology is environmentally friendly. It reduces material waste and consumes less energy compared to traditional cutting methods, making it a sustainable choice for modern manufacturing.
By embracing laser cutting and engraving, you unlock endless possibilities. You can bring your most ambitious designs to life with precision and ease. This technology not only enhances your production capabilities but also inspires innovation in every project you undertake.
Materials Used in Precision Machining
The choice of materials plays a critical role in precision machining. Each material brings unique properties that make it suitable for specific applications. Whether you’re working with metals, plastics, or composites, selecting the right material ensures your components meet the highest standards of performance and durability.
Metals
Metals are the backbone of precision machining. Their strength, durability, and versatility make them ideal for creating high-performance components. Here are some of the most commonly used metals:
Aluminum
Aluminum is lightweight yet strong, making it a favorite in industries like aerospace and automotive. Its excellent machinability allows you to achieve tight tolerances with ease. Aluminum also resists corrosion, ensuring long-lasting performance. You’ll find it used in everything from aircraft parts to electronic enclosures.
Steel
Steel offers unmatched toughness and versatility. Stainless steel, in particular, stands out for its machinability and corrosion resistance. Grades like SS303, SS304, and SS316 each bring unique properties. For example, SS316 excels in harsh environments due to its superior resistance to chemicals and saltwater. Steel’s strength and durability make it indispensable in heavy-duty applications like construction and machinery.
Titanium
Titanium combines strength with a lightweight structure, making it essential for industries like aerospace and medical devices. Its biocompatibility ensures safety in implants and surgical tools. Titanium also withstands extreme temperatures, making it perfect for jet engines and spacecraft components.
Other metals like brass also shine in precision machining. Brass is soft and easy to machine, even without lubrication. Its corrosion resistance and antibacterial properties make it ideal for plumbing fixtures and medical applications.
Plastics
Plastics bring a unique set of advantages to precision machining. Their versatility allows you to create components for industries ranging from aerospace to food processing. Here’s why plastics stand out:
- Mechanical strength ensures durability in demanding applications.
- Thermal stability maintains dimensional accuracy under temperature changes.
- Chemical resistance protects against harsh environments, including exposure to acids and solvents.
Plastics like PEEK, PTFE, and nylon are popular choices. PEEK offers exceptional strength and heat resistance, making it ideal for aerospace and medical applications. PTFE, known for its low friction, works well in seals and gaskets. Nylon provides excellent wear resistance, perfect for gears and bearings.
However, plastics require careful handling during machining. Their higher coefficient of thermal expansion can lead to dimensional changes when heated. Understanding these properties helps you achieve precise results.
Composites and Ceramics
Composites and ceramics push the boundaries of what’s possible in precision machining. These materials combine strength, heat resistance, and lightweight properties, making them ideal for advanced applications.
- Composites: Carbon fiber composites are incredibly strong yet lightweight. They’re perfect for aerospace and automotive parts where weight reduction is critical. Their resistance to fatigue and corrosion ensures long-term reliability.
- Ceramics: Ceramics like zirconia and alumina excel in high-temperature environments. Their hardness and wear resistance make them ideal for cutting tools and medical implants. Ceramics also resist chemical attacks, ensuring durability in harsh conditions.
By choosing the right material, you unlock the full potential of precision machining. Each material brings unique strengths, allowing you to create components that meet the most demanding requirements.
Benefits of Precision Machining
Tight Tolerances and High Precision
Precision machining allows you to achieve incredibly tight tolerances and unmatched precision. This capability ensures that every component meets exact specifications, which is critical in industries where even the smallest deviation can lead to failure. For example, aerospace components demand much tighter tolerances than traditional machining methods can provide. Similarly, medical devices require extreme accuracy to ensure patient safety and functionality.
Tolerances define the acceptable limits of variation in the dimensions of a part. Precision machining excels in meeting these stringent requirements. Here’s a quick comparison of tolerances achievable with different materials:
Material Type | Tolerance Achievable |
---|---|
Metals | ±0.127 mm |
Plastics | ±0.01 inches |
By using advanced tools and techniques, you can create parts that fit together seamlessly, ensuring flawless performance. Whether you’re crafting intricate aerospace components or life-saving medical devices, precision machining guarantees the highest level of accuracy.
Cost-Effectiveness in Manufacturing
Precision machining doesn’t just deliver quality; it also saves you money. By automating production processes, CNC machining reduces cycle times and labor costs. You’ll notice fewer errors and defects, which means less rework and lower expenses. Additionally, precise cuts minimize material waste, helping you save on raw materials.
Here are some ways precision machining contributes to cost-effectiveness:
- Improved Production Efficiency: Automation speeds up production, allowing you to meet tight deadlines.
- Minimized Material Waste: Accurate machining reduces scrap, making your operations more sustainable.
- Reduced Labor Costs: Fewer operators are needed, freeing up resources for other tasks.
- Lower Tooling Costs: CNC machines can handle multiple applications with the same tools.
- Faster Prototyping: Quick iterations help you bring products to market faster.
- Customization and Flexibility: Easily reprogram machines for new designs, cutting down on retooling expenses.
By embracing precision machining, you not only enhance product quality but also optimize your manufacturing budget. It’s a smart investment that pays off in both the short and long term.
Repeatability and Consistency in Production
Precision machining ensures that every part you produce is identical to the last. This level of repeatability is essential in industries where consistency is non-negotiable. For example, the automotive sector relies on precision machining to create intricate gears and engine components. The medical industry uses it to manufacture tools and equipment for complex surgeries. Aerospace applications demand consistent quality to meet strict safety standards.
Here’s a look at how different industries benefit from repeatability:
Industry |
Application |
---|---|
Automobiles | Requires intricate gears and components for engine parts, axles, etc. |
医疗行业 | Needs automated tools and equipment for complex surgeries and procedures. |
航空航天 | Utilizes advanced equipment and materials requiring high accuracy machining. |
Defense Industry | Demands rugged materials and quality precision machining for various systems. |
When you rely on precision machining, you can trust that every component will meet your exact specifications. This consistency reduces defects, enhances product reliability, and builds trust with your customers. It’s the foundation of efficient, high-quality production.
Versatility Across Materials and Applications
Precision machining stands out for its incredible versatility. It adapts to a wide range of materials and applications, making it a cornerstone of modern manufacturing. Whether you’re working with metals, plastics, or advanced composites, precision machining empowers you to create components that meet the highest standards of performance and durability.
You’ll find this adaptability invaluable across industries. Each sector benefits from the unique capabilities of precision machining:
- 汽车: Precision machining produces intricate gears, axles, and engine components. These parts demand tight tolerances to ensure vehicles run smoothly and efficiently.
- 医疗行业: Micro-level machining creates surgical tools, implants, and diagnostic equipment. These devices require extreme accuracy to safeguard patient safety and improve outcomes.
- 航空航天: Advanced materials like titanium and carbon fiber composites are machined into lightweight, high-strength parts. Precision machining ensures these components meet strict tolerances for safety and performance.
- Defense Industry: Rugged materials are transformed into weapons prototypes, missile systems, and other critical components. Precision machining delivers the reliability and durability needed in high-stakes applications.
This versatility doesn’t stop at industries. Precision machining also excels in handling diverse materials. Metals like aluminum, steel, and titanium offer strength and durability. Plastics provide lightweight solutions with excellent chemical resistance. Composites and ceramics push the boundaries of innovation, combining strength, heat resistance, and lightweight properties.
Imagine the possibilities when you can work with such a wide variety of materials. You can create lightweight aerospace parts, durable medical implants, or even intricate electronic components. Precision machining gives you the freedom to explore new designs and applications without limitations.
The ability to adapt to different materials and industries makes precision machining a powerful tool for innovation. It allows you to meet the unique demands of each project while maintaining the highest standards of quality. Whether you’re crafting life-saving medical devices or cutting-edge aerospace components, precision machining ensures your vision becomes reality.
Tip: When choosing materials for precision machining, consider the specific requirements of your application. The right material can enhance performance, reduce costs, and ensure long-term reliability.
By embracing the versatility of precision machining, you unlock endless opportunities. It’s not just about creating parts; it’s about pushing boundaries and achieving what once seemed impossible. With precision machining, you hold the key to innovation across industries and materials. 🌟
Applications of Precision Machining
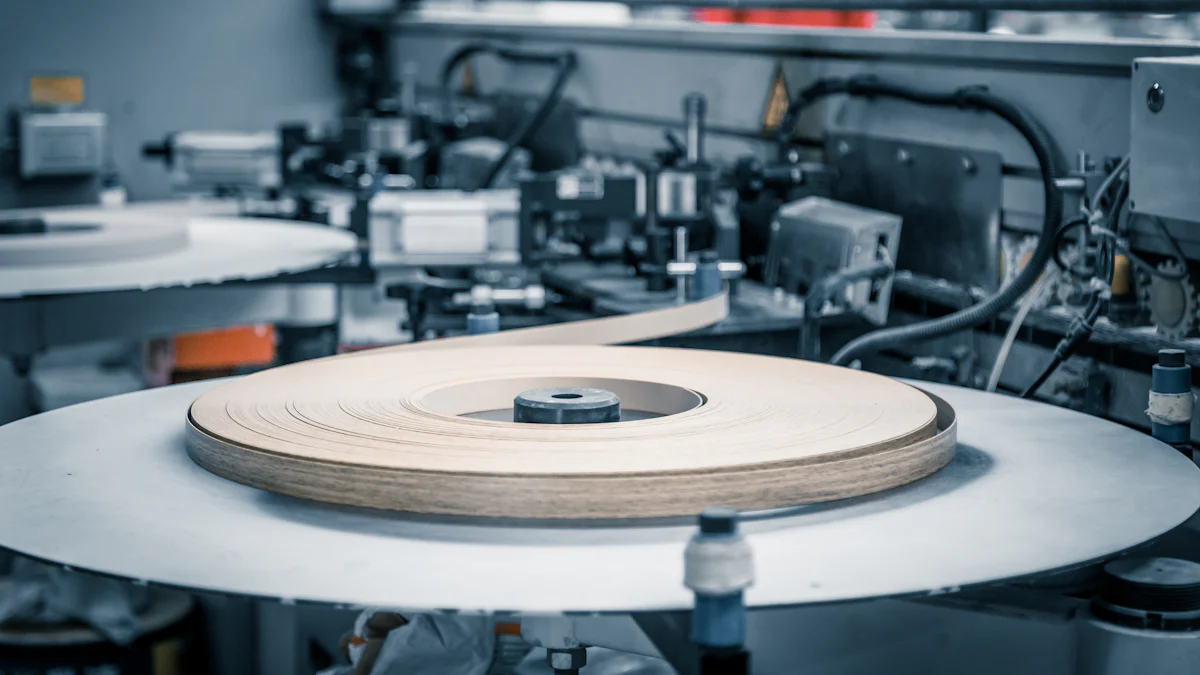
航空航天工业
In the aerospace industry, every component must meet the highest standards of precision and reliability. You rely on precision machining to create parts that perform flawlessly under extreme conditions. Advanced techniques like CNC machining, flow forming, and rotary forging ensure that components meet strict tolerances and specifications. These processes allow you to achieve the accuracy required for critical parts like turbine blades, landing gear, and structural components.
The use of advanced materials, such as carbon-fiber-reinforced polymers (CFRP), further enhances performance. These materials reduce the weight of aircraft while maintaining structural integrity. This weight reduction improves fuel efficiency and reduces emissions, making air travel more sustainable. Precision machining empowers you to push the boundaries of aerospace innovation, ensuring safety and efficiency in every flight.
Automotive Sector
Precision machining plays a vital role in the automotive sector, where accuracy and durability are non-negotiable. You depend on this technology to produce high-quality components that meet rigorous safety standards. Techniques like CNC machining and precision grinding allow you to create complex parts with exceptional accuracy. These methods enhance production efficiency and ensure that every component meets your exact specifications.
Engine parts, transmission components, and suspension systems are just a few examples of where precision machining shines. By achieving tight tolerances, you improve vehicle performance and durability. Modern techniques also enable you to meet the growing demand for electric vehicles, where precision is critical for battery systems and lightweight designs. With precision machining, you can drive innovation and deliver vehicles that perform better and last longer.
Medical Devices and Equipment
In the medical field, precision machining is a cornerstone of innovation and safety. You rely on it to create devices that meet exact specifications, ensuring patient safety and effective treatment. CNC machining allows you to produce customized implants and tools tailored to individual needs. This level of customization improves outcomes and enhances the quality of care.
Durability is another key benefit. Precision machining ensures that medical devices are robust and long-lasting, even in demanding environments like the human body. From surgical instruments to diagnostic equipment, every component must perform flawlessly. By embracing precision machining, you contribute to life-saving advancements and help improve the lives of countless patients.
Electronics and Semiconductors
Precision machining plays a transformative role in the world of electronics and semiconductors. As technology advances, you see devices becoming smaller, faster, and more powerful. This evolution demands components with exceptional precision and reliability. Precision machining meets these challenges head-on, enabling you to create parts that push the boundaries of innovation.
In the semiconductor industry, precision machining ensures that components can withstand severe electrostatic discharge (ESD) events. This durability extends maintenance intervals and improves output consistency. These qualities are essential as manufacturers strive to meet the growing demand for smaller and more intricate designs in modern electronics. Whether it’s a smartphone, a stereo system, or a cutting-edge computer, precision machining ensures every part functions flawlessly.
Here’s how precision machining benefits electronics and semiconductors:
- It enables the creation of components with tight tolerances, ensuring functionality and reliability.
- It improves assembly compatibility, so parts fit together seamlessly without gaps or overhangs.
- High-quality parts manufactured to close tolerances add value to products, allowing you to command higher prices.
Tip: When designing electronic components, focus on precision. It enhances performance and ensures your products stand out in a competitive market.
Precision machining also supports the production of advanced materials used in semiconductors. These materials require intricate machining to achieve the exact specifications needed for high-performance devices. By embracing this technology, you can stay ahead in an industry that thrives on innovation and precision.
Energy and Power Generation
In the energy sector, precision machining powers progress. Whether you’re working with traditional power plants or renewable energy systems, precision components are essential for efficiency and reliability. Turbines, compressors, pumps, and generators all rely on parts crafted with exceptional accuracy. These components ensure that energy systems operate smoothly, minimizing downtime and maximizing output.
For power plants, precision machining creates turbine systems capable of withstanding extreme conditions. These turbines convert energy into electricity with remarkable efficiency. In renewable energy, precision machining enables the production of intricate parts for wind turbines and solar panels. These components must meet strict tolerances to ensure optimal performance and durability.
Here are some key applications of precision machining in energy and power generation:
- Turbine Systems: Precision components improve efficiency and reduce wear in power plants.
- Renewable Energy Systems: Intricate parts enhance the performance of wind and solar technologies.
- Compressors and Pumps: High-precision parts ensure smooth operation and long-term reliability.
- Generators: Accurate machining supports consistent energy production.
Note: By investing in precision machining, you contribute to a more sustainable future. High-quality components reduce waste and improve energy efficiency.
Precision machining doesn’t just support energy production; it drives innovation. As the world shifts toward cleaner energy sources, you can rely on this technology to create the components needed for a greener tomorrow. Whether it’s a wind turbine blade or a high-efficiency pump, precision machining ensures every part performs at its best.
The Future of Precision Machining
Advancements in Automation and AI
The future of precision machining is being shaped by groundbreaking advancements in automation and artificial intelligence (AI). These technologies are revolutionizing how you approach manufacturing, making processes faster, smarter, and more efficient. Imagine a world where machines think ahead, predict wear, and optimize their own performance. This is no longer a dream but a reality.
AI and machine learning now optimize tool paths and predict tool wear, ensuring consistent quality in every part you produce. With IoT-enabled real-time monitoring systems, you gain valuable insights into machine performance and maintenance needs. This means fewer unexpected downtimes and smoother operations. Enhanced CAD/CAM systems streamline the design-to-production workflow, saving you time and reducing errors.
You’ll also notice how robotics is transforming CNC machining. Automated tool changes and material handling improve production speed while reducing human error. IoT integration allows machines to share real-time data, optimizing maintenance schedules and operational efficiency. These advancements empower you to produce complex parts faster and with greater precision than ever before.
Integration with Additive Manufacturing
The integration of precision machining with additive manufacturing is unlocking new possibilities in design and production. Additive manufacturing, often known as 3D printing, builds intricate structures layer by layer. When combined with precision machining, it creates a powerful synergy that enhances your capabilities.
This integration offers several benefits:
Benefits of Integration |
---|
Enhanced design freedom |
Reduced material waste |
Faster prototyping capabilities |
Production of complex geometries |
You can now create lightweight components with optimized topologies, perfect for industries like aerospace and automotive. This approach accelerates product development cycles, helping you bring innovative designs to market faster. By combining the strengths of both technologies, you achieve unmatched precision and efficiency in manufacturing.
Focus on Sustainability and Eco-Friendly Practices
Sustainability is becoming a cornerstone of modern precision machining. As you look to the future, adopting eco-friendly practices not only benefits the planet but also enhances your business’s reputation and efficiency.
Energy-efficient machine tools are leading the way, consuming less power and reducing costs. By using biodegradable materials and recycled metals, you contribute to conserving natural resources. Recycling programs for metal scraps and coolant minimize waste, ensuring that valuable materials are reused. Dry machining techniques and alternative coolants reduce the need for excessive coolant usage, conserving resources further.
Renewable energy sources like solar and wind are also powering machining processes, lowering reliance on non-renewable energy. These practices not only reduce your environmental impact but also align with the growing demand for sustainable manufacturing. By embracing these changes, you position yourself as a leader in eco-friendly innovation.
The future of precision machining is bright, driven by automation, additive manufacturing, and sustainability. These advancements inspire you to push boundaries, innovate boldly, and create a better world through smarter manufacturing.
Emerging Applications in New Industries
Precision machining is breaking barriers and finding its way into industries that demand innovation and accuracy. You’ll see its influence growing in areas where precision and reliability are essential. These emerging applications are shaping the future and opening doors to endless possibilities.
In healthcare, precision machining is revolutionizing the way surgical tools and medical devices are made. The industry is moving toward minimally invasive procedures, which require tools with intricate designs and tight tolerances. You can rely on precision machining to create these tiny, complex components. For example, implants and diagnostic devices must meet exact specifications to ensure safety and effectiveness. This technology empowers you to deliver life-saving solutions with unmatched accuracy.
The automotive sector is another area where precision machining is making waves. As electric vehicles (EVs) gain popularity, the demand for high-precision components is skyrocketing. You’ll notice that EVs require lightweight yet durable parts for engines, transmissions, and battery systems. Precision machining helps you meet these needs by producing components that enhance performance and efficiency. This innovation is driving the future of sustainable transportation.
In aerospace and defense, precision machining plays a critical role in creating lightweight and durable components. You’ll find it essential for manufacturing turbine blades, landing gear, and structural parts. These components must adhere to strict safety standards while performing under extreme conditions. Precision machining allows you to achieve the reliability and strength needed for these high-stakes applications. It’s a game-changer for industries that demand perfection.
Beyond these established sectors, precision machining is also paving the way for advancements in renewable energy. Wind turbines and solar panels rely on intricate parts to maximize efficiency. You can use precision machining to craft these components with the accuracy required for optimal performance. This technology supports the transition to cleaner energy sources, contributing to a more sustainable future.
The possibilities don’t stop there. As industries evolve, you’ll see precision machining unlocking new opportunities in robotics, biotechnology, and even space exploration. Its ability to deliver flawless results makes it a cornerstone of innovation. By embracing this technology, you position yourself at the forefront of progress, ready to tackle the challenges of tomorrow.
Tip: Stay ahead by exploring how precision machining can transform your industry. The future belongs to those who innovate boldly and embrace change. 🌟
Precision machining stands as a cornerstone of modern manufacturing, shaping industries with its unparalleled accuracy and versatility. It creates components with tolerances measured in micrometers, ensuring safety and performance in critical fields like aerospace and medical devices. You can rely on its repeatability to deliver consistent results, even in mass production. Its ability to work with diverse materials unlocks endless possibilities for innovation.
This technology also accelerates prototyping, allowing you to test and refine designs with precision. As advancements like AI, real-time monitoring, and sustainable materials emerge, the future of precision machining promises even greater efficiency and creativity. By embracing these innovations, you position yourself at the forefront of manufacturing excellence.
FAQ
What is the main purpose of precision machining?
Precision machining creates parts with exact dimensions and tight tolerances. It ensures components fit perfectly and function reliably. You’ll find it essential in industries like aerospace, medical devices, and automotive, where accuracy and quality are critical for safety and performance.
How does precision machining reduce waste?
Precision machining minimizes material waste by using advanced tools and techniques. It removes only the necessary material, ensuring efficient use of resources. You’ll also benefit from reduced scrap and rework, which saves costs and supports sustainable manufacturing practices.
Can precision machining handle complex designs?
Yes! Precision machining excels at producing intricate and complex designs. Multi-axis CNC machines and advanced software allow you to create parts with detailed geometries. This capability supports innovation in industries like aerospace, healthcare, and electronics.
What materials can be used in precision machining?
Precision machining works with metals like aluminum, steel, and titanium. It also handles plastics, composites, and ceramics. Each material offers unique properties, so you can choose the one that best suits your application’s requirements for strength, durability, or heat resistance.
Why is precision machining important for medical devices?
Medical devices require extreme accuracy to ensure patient safety and effectiveness. Precision machining creates implants, surgical tools, and diagnostic equipment with tight tolerances. This technology allows you to produce customized solutions that improve outcomes and enhance the quality of care.
How does CNC machining improve efficiency?
CNC machining automates production, reducing human error and speeding up processes. You’ll benefit from consistent quality, faster cycle times, and lower labor costs. Its ability to handle complex tasks with precision makes it a cornerstone of modern manufacturing.
Is precision machining cost-effective?
Absolutely! Precision machining reduces material waste, minimizes errors, and automates production. These factors lower costs while maintaining high quality. You’ll also save time with faster prototyping and production, making it a smart investment for any manufacturing project.
What industries benefit most from precision machining?
Industries like aerospace, automotive, medical, and electronics rely heavily on precision machining. It ensures high-quality components for critical applications. You’ll also see its growing impact in renewable energy, robotics, and space exploration as technology advances.
Tip: Explore how precision machining can transform your industry. Its versatility and accuracy open doors to endless possibilities! 🌟