Comparing CNC Machining and Sand Casting
Explore the differences between CNC machining and sand casting for manufacturing needs.
Features | CNC machining | sand casting |
---|---|---|
Precision and accuracy | Achieves tolerances as tight as +/- 0.0002”. | Offers broader tolerances, less suitable for tight specifications. |
Material compatibility | Works with metals, plastics, and composites. | Supports high-melting-point materials like steel and titanium. |
Production speed | Faster for small batches and prototypes. | Efficient for large-scale production after mold setup. |
Cost considerations | Lower setup costs, higher per-unit cost for large runs. | Higher setup costs, lower per-unit cost for large runs. |
Scalability and volume | Ideal for small batches and prototyping. | Better for large-scale production and mass manufacturing. |
Design complexity | Excels in intricate and precise designs. | Handles complex shapes but with less precision. |
Surface finish | Produces smooth and polished finishes. | Results in rougher finishes requiring post-processing. |
Tooling requirements | Requires no molds, uses cutting tools. | Needs molds, increasing initial setup time. |
Environmental impact | Generates material waste from cutting. | Reuses sand molds, reducing material waste. |
Application suitability | Best for precision-critical industries like aerospace. | Ideal for automotive and large industrial parts. |
Choosing the right manufacturing method can significantly impact your project’s success. CNC machining and sand casting are two popular techniques, each offering unique advantages. CNC machining uses precise tools to remove material from a workpiece, delivering exceptional accuracy. In contrast, sand casting involves pouring molten metal into sand molds, making it ideal for intricate designs and high-melting-point alloys like titanium and steel.
Understanding these methods helps you make informed decisions. Factors such as design complexity, material selection, and production volume play a crucial role. For example, machining excels in precision, while casting suits large-scale production. Evaluating these aspects ensures you select the best approach for your needs.
Key Takeaways
- CNC machining is very precise. It can be accurate to 0.0002 inches. This is great for projects needing exact details.
- Sand casting is good for making many items. Once you have the molds, you can make parts quickly. This lowers the cost for each item.
- Use CNC machining for small amounts or test pieces. It needs less setup and no molds, saving money for small jobs.
- Pick sand casting for tricky shapes and big parts. It lets you design freely and works with materials that melt at high temperatures.
- Think about what your project needs. Look at things like accuracy, how many you need, and how complex the design is to pick the best way.
Understanding CNC machining
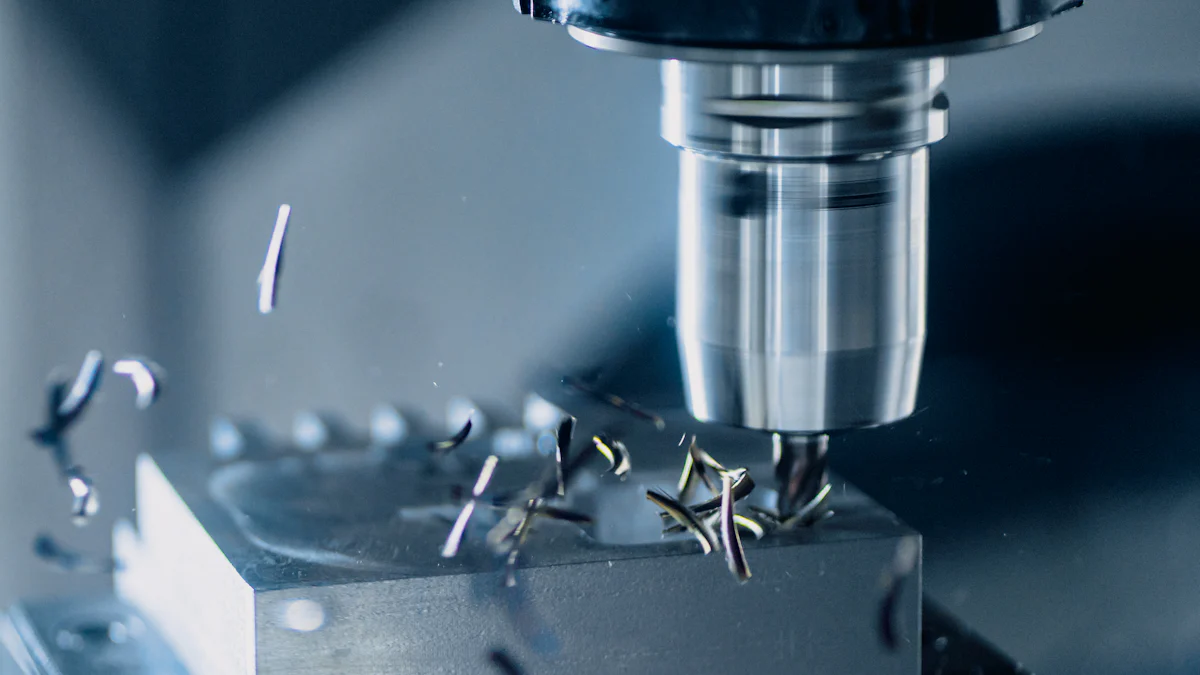
Overview of the CNC machining process
CNC machining involves several precise steps to transform raw materials into finished parts. Here’s how the process unfolds:
- Material Preparation: You start by selecting and preparing the raw material.
- CAD/CAM Programming: You create a digital design using CAD software, which is then converted into a machine-readable format.
- Machine Setup: You set up the CNC machine with the necessary tools and load the program.
- Machining Execution: The machine removes material from the workpiece to form the desired shape.
- Inspection and Quality Control: You inspect the final product to ensure it meets the required specifications.
Key characteristics of CNC machining
CNC machining stands out due to its unique features:
- High accuracy and precision: You achieve tight tolerances and produce highly accurate parts.
- Increased production efficiency: Automation speeds up production and reduces cycle times.
- Versatility and flexibility: You can perform various machining operations and handle complex geometries.
- Repetitive and consistent results: The process ensures identical parts with minimal human error.
- Design freedom and complexity: You can create intricate designs that are challenging with traditional methods.
Technological advancements have further enhanced CNC machining. Automation improves part quality and repeatability. Robotics integration boosts production speed and reduces errors. IoT connectivity allows real-time data sharing, while high-resolution sensors enhance accuracy.
Common materials used in CNC machining
CNC machining accommodates a wide range of materials, each offering distinct advantages:
- Aluminum: Known for its high machinability, lightweight nature, and corrosion resistance.
- Stainless Steel: Offers excellent wear and corrosion resistance, though it’s harder to machine.
- Carbon Steel: Provides superior strength and machinability at a reasonable cost.
- Copper: Valued for its thermal and electrical conductivity, ideal for electrical applications.
- Titanium: Features a high strength-to-weight ratio, perfect for aerospace and medical uses.
- Acrylic: Offers high optical clarity and rigidity, suitable for various applications.
- Nylon: Strong and impact-resistant, ideal for parts needing friction protection.
These materials make CNC machining a versatile choice for diverse applications.
Understanding sand casting
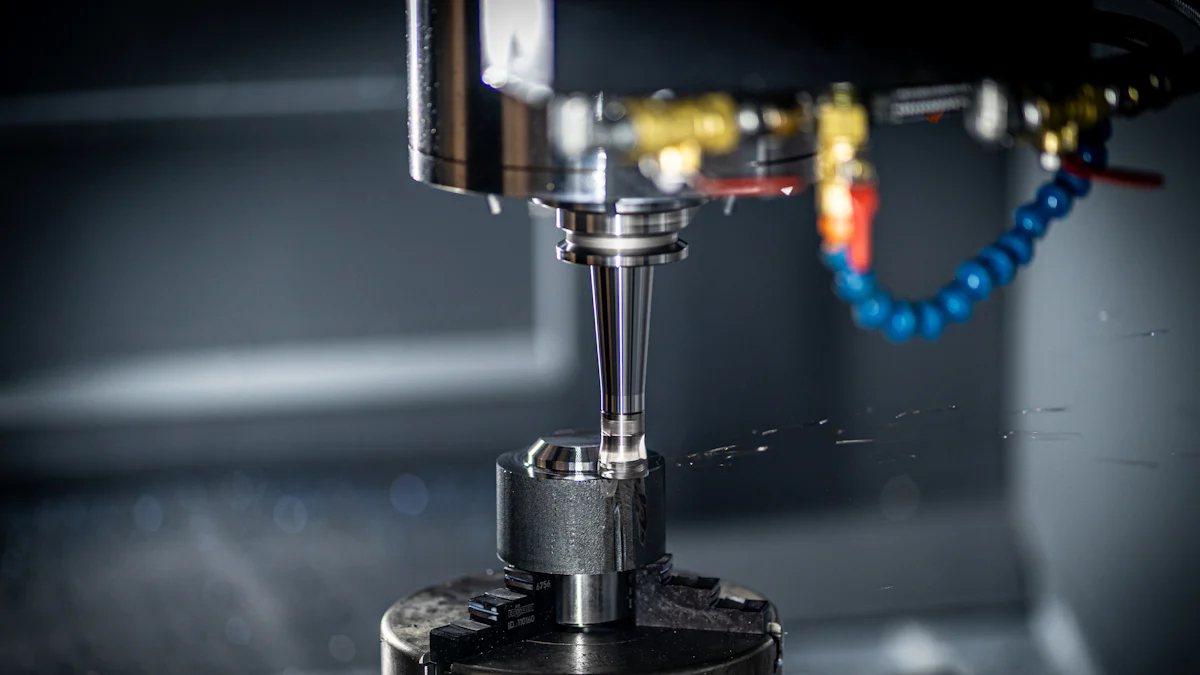
Overview of the sand casting process
Sand casting transforms molten metal into solid parts using sand molds. This process involves several steps:
- Place Mold Pattern in Sand: You begin by placing a pattern in sand to create a cavity.
- Set Up the Gating System: A gating system is added to guide molten metal into the mold.
- Remove the Mold Pattern: The pattern is carefully removed, leaving a hollow cavity.
- Pour Molten Metal Into Mold Cavity: You pour molten metal into the cavity through the gating system.
- Wait for Metal to Cool: The metal cools and solidifies within the mold.
- Break Open Mold to Remove the Metal Casting: Finally, you break the mold to retrieve the casting.
Recent advancements, such as 3D-printed molds, have revolutionized this process. These technologies reduce lead times and improve precision, making sand casting more efficient and cost-effective.
Key characteristics of sand casting
Sand casting stands out for its versatility and adaptability. You can use it to produce parts of various sizes and complexities. This method is especially effective for creating intricate shapes that other techniques may struggle to achieve. It also supports a wide range of materials, offering flexibility in design.
Sand casting is a low-cost solution, particularly for low-volume production. However, its cost-effectiveness may decrease when scaling up to thousands of castings.
Technological innovations, such as digital modeling and additive manufacturing, have further enhanced sand casting. These advancements allow for more complex designs, reduce material waste, and improve sustainability.
Common materials used in sand casting
Sand casting accommodates a variety of materials, each chosen for specific properties:
- Green Sand: A mix of sand, clay, and water, offering flexibility and good dimensional stability.
- Resin Sand: Uses synthetic resin binders for stronger molds and smoother finishes.
- Silica Sand: Affordable and capable of withstanding high temperatures, making it widely used.
- Chromite Sand: Known for high thermal conductivity, ideal for high-performance alloys.
- Zircon Sand: Offers low thermal expansion, ensuring precise castings.
These materials make sand casting a reliable choice for industries like automotive, aerospace, and general manufacturing. You can select the material that best suits your project’s requirements.
CNC machining vs sand casting: A detailed comparison
Precision and accuracy
Tolerances achievable with CNC machining
CNC machining delivers exceptional precision, making it ideal for applications requiring tight tolerances. You can achieve tolerances as tight as +/- 0.0002” (0.00508 mm). This level of accuracy ensures that parts meet exact specifications, even for complex designs. The repeatability of CNC machining also guarantees consistent results across multiple production runs.
Tolerances achievable with sand casting
Sand casting, while versatile, typically offers broader tolerances. This method is less suitable for projects requiring exact dimensions. The inherent nature of sand molds limits the precision achievable, making it better suited for applications where tight tolerances are not critical.
CASTING | CNC Machining | |
---|---|---|
Precision | Typically broader tolerances, less ideal for tight specifications. | Achieves tolerances as tight as +/- 0.0002” (0.00508 mm), ideal for exact dimensions. |
Material compatibility
Materials suitable for CNC machining
CNC machining works well with a wide range of materials. Softer materials, such as aluminum and acrylic, are easier to machine. However, tougher materials like stainless steel and titanium are also compatible, provided the right tools are used. You can select materials based on the required strength, toughness, and machinability of your project.
Materials suitable for sand casting
Sand casting accommodates materials with high melting points, such as steel and titanium. This method is ideal for creating intricate shapes and large parts. The choice of material depends on factors like melting temperature, casting quality, and the complexity of the design. For example, chromite sand is preferred for high-performance alloys due to its thermal conductivity.
Tip: Consider the complexity of your design and the material’s properties when choosing between CNC machining and sand casting.
Production speed
Setup time for CNC machining
CNC machining requires significant setup time. You need to prepare the material, program the machine, and set up the tools. However, once the setup is complete, the process is efficient for small batches and prototypes. This makes CNC machining a faster option for low-volume production.
Setup time for sand casting
Sand casting involves preparing molds, which can take longer than CNC machining setup. However, once the molds are ready, the process becomes highly efficient for large-scale production. This method is particularly advantageous when producing large quantities of parts quickly.
Note: For small batches, CNC machining offers shorter lead times. For high-volume production, sand casting becomes more time-efficient.
Cost considerations
Initial setup costs
When considering initial setup costs, CNC machining offers a clear advantage. You do not need molds or specialized tooling, which keeps upfront expenses low. This makes CNC machining an excellent choice for projects with limited budgets or short lead times. On the other hand, sand casting requires the creation of molds, which can significantly increase initial costs. These molds, often made from sand and binders, involve both material and labor expenses. However, once the molds are created, they can be reused, spreading the cost over multiple parts.
Per-unit production costs
The per-unit cost of CNC machining depends on factors like material type, machining time, and tool wear. For small production runs, CNC machining remains cost-effective due to its lack of preparatory tooling. However, as production volumes increase, the cost per unit does not decrease significantly. Sand casting, in contrast, becomes more economical with higher production volumes. The fixed costs, such as mold creation, get distributed across a larger number of parts, reducing the cost per unit. This makes sand casting a better option for high-volume production where cost efficiency is critical.
Tip: If your project involves a small batch or prototype, CNC machining minimizes upfront costs. For large-scale production, sand casting offers better cost efficiency.
Scalability and production volume
Small-batch production
CNC machining excels in small-batch production. You can quickly set up the process without the need for molds or extensive preparation. This allows you to produce dozens to a few thousand parts efficiently. The precision and flexibility of CNC machining also make it ideal for prototyping and custom designs. Sand casting, however, is less suited for small batches due to the time and cost involved in mold preparation. The high initial setup costs make it less economical for limited production runs.
Large-scale production
For large-scale production, sand casting becomes the more efficient option. Once the molds are ready, the process allows you to produce parts at a high rate. The cost per unit decreases significantly as production volume increases, making it a cost-effective solution for thousands of parts. CNC machining, while precise, struggles to match the speed and cost efficiency of sand casting for large-scale runs. The lack of reusable tooling in CNC machining means that costs remain relatively constant, regardless of production volume.
Note: Choose CNC machining for small batches or prototypes. Opt for sand casting when scaling up to large production volumes.
Choosing the right method for your needs
When to choose CNC machining
Applications requiring high precision
You should choose CNC machining when your project demands exceptional precision and tight tolerances. This method excels in industries like automotive, aerospace, and medical devices, where accuracy is critical. For example, in the automotive sector, CNC machining ensures consistent quality for large production volumes. In aerospace, it produces complex parts with tight tolerances. Medical devices, such as surgical instruments and implants, also rely on CNC machining for its ability to meet strict quality standards.
Industry | Scenario Description |
---|---|
Automotive | Requires high precision, large production volumes, and consistent quality. |
Aerospace | Demands the ability to produce complex parts with tight tolerances. |
Medical Devices | Needs high precision and adherence to strict quality standards for surgical instruments and implants. |
Prototyping and small-batch production
CNC machining is ideal for prototyping and small-batch production. You can quickly set up the process without the need for molds, making it cost-effective for limited runs. This method allows you to test designs and make adjustments before committing to large-scale production. Its precision ensures that prototypes closely match the final product, reducing the risk of errors in later stages.
When to choose sand casting
Applications requiring large-scale production
Sand casting becomes the better choice when you need to produce large quantities of parts. Once the molds are prepared, this method allows for high production rates. The cost per unit decreases significantly as production volume increases, making it a cost-efficient solution for mass production. Sand casting also supports a wide range of materials, including those with high melting points, which adds to its versatility.
Complex shapes and large parts
You should consider sand casting for projects involving intricate shapes or large components. This method offers high design flexibility, allowing you to create complex geometries that other techniques may struggle to achieve. It is also effective for producing large parts, such as engine blocks or industrial machinery components. Sand casting accommodates both small-scale and large-scale production, making it suitable for a variety of manufacturing needs.
Tip: Evaluate your project’s requirements for precision, production volume, and design complexity to determine whether CNC machining or sand casting is the better fit.
Understanding the differences between CNC machining and sand casting helps you make informed decisions. CNC machining delivers unmatched precision with tolerances as tight as +/- 0.0002” (0.00508 mm). It produces smooth finishes, making it ideal for high-precision applications. Sand casting, on the other hand, excels in high-volume production, though it may result in rougher finishes.
When choosing a method, consider your project’s needs:
- Opt for CNC machining for low-volume production or when tight tolerances are critical.
- Choose sand casting for large-scale production or complex, large parts.
Evaluate factors like precision, cost, and production volume to select the best approach for your goals.
FAQ
What is the main difference between CNC machining and sand casting?
CNC machining removes material to create parts with high precision. Sand casting pours molten metal into molds to form parts. CNC machining suits tight tolerances, while sand casting works better for large-scale production and complex shapes.
Which method is more cost-effective for small batches?
CNC machining is more cost-effective for small batches. It does not require molds, reducing initial setup costs. Sand casting involves mold preparation, which increases expenses for limited production runs.
Can both methods handle complex designs?
Yes, both methods can handle complex designs. CNC machining excels in creating intricate details with precision. Sand casting allows for complex geometries but may lack the same level of accuracy.
Which method is faster for prototyping?
CNC machining is faster for prototyping. You can quickly set up the process without molds. Sand casting takes longer due to mold preparation and cooling times.
Are there material limitations for CNC machining and sand casting?
CNC machining works with metals, plastics, and composites. Sand casting supports materials with high melting points, like steel and titanium. Your choice depends on the material’s properties and project requirements.